Cost-Effectiveness
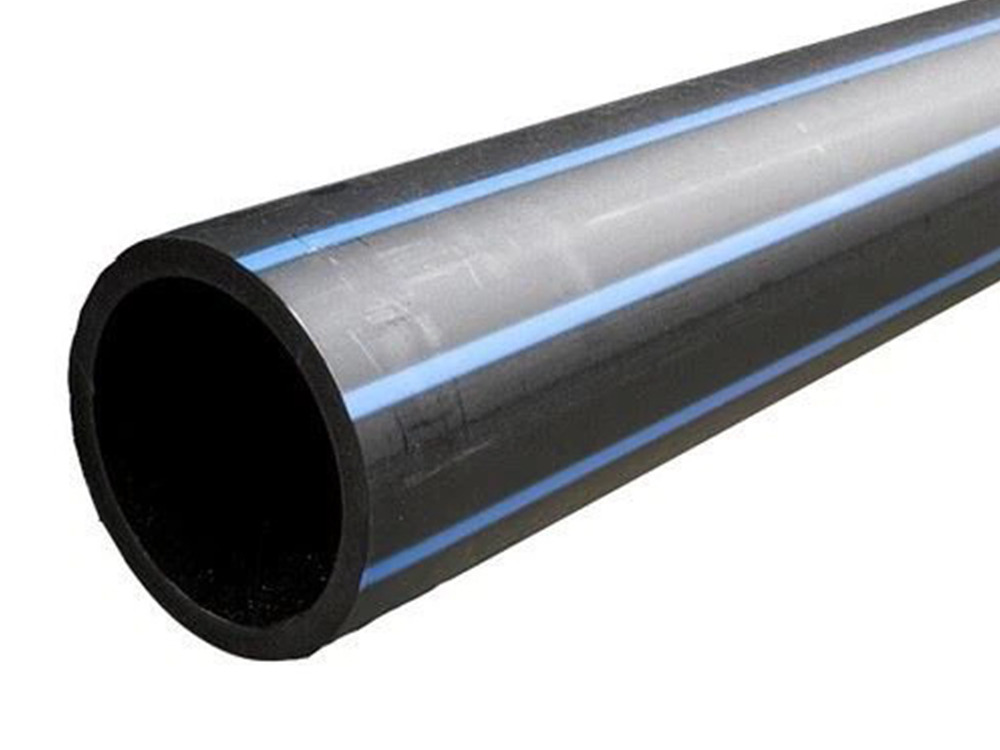
Lower Maintenance Costs
HDPE pipes offer significant savings in maintenance due to their durability and resistance to corrosion. Unlike traditional materials such as steel, HDPE pipes do not rust or degrade when exposed to harsh chemicals or environmental conditions. Their smooth interior surface minimizes buildup, reducing the likelihood of blockages and leaks. This reliability translates into fewer repairs and lower operational costs over time. For example, HDPE pipes used in wastewater systems maintain their structural integrity even under high-pressure conditions, ensuring long-term performance with minimal upkeep.
Long-Term Savings
Although HDPE pipes may have higher upfront costs compared to alternatives like mild steel, they provide substantial long-term financial benefits. A comparative analysis of pipeline projects revealed that an HDPE pipeline costing $129,382 had a significantly lower total expense than a mild steel pipeline, which exceeded $299,000. The extended lifespan of HDPE pipes, ranging from 50 years, further enhances their cost-effectiveness by reducing the frequency of replacements and associated labor costs.
Material | Lifespan (Years) | Initial Cost (USD) | Long-Term Cost (USD) |
HDPE Pipes | 50-100 | 129,382 | 129,382 |
Mild Steel Pipes | 40-50 | 299,000 | 299,000 + maintenance |
Versatility in Applications
Use in Water Distribution and Sewage Systems
HDPE pipes excel in water distribution and sewage systems due to their leak-free joints and resistance to biological growth. They are widely used for transporting potable water in cities and rural areas, ensuring safe and efficient delivery. In sewage systems, HDPE pipes handle both force main and gravity flow applications, withstanding harsh conditions such as cold weather and seismic activity. Their heat-fused joints prevent leaks, making them ideal for large-scale infrastructure projects. Additionally, reclaimed water systems benefit from HDPE pipes by diverting treated wastewater for agricultural and industrial use.
Applications in Industrial Piping and Gas Distribution
The chemical resistance of HDPE pipes makes them suitable for industrial piping systems, where they transport aggressive substances without degradation. In the oil and gas sector, these pipes are used for transmitting natural gas, crude oil, and produced water. Their flexibility and lightweight design simplify installation in challenging terrains, such as offshore platforms and mountainous regions. This adaptability ensures that HDPE pipes meet the diverse needs of industrial and municipal projects.
Environmental Sustainability
Reduced Carbon Footprint
HDPE pipes contribute to sustainability by reducing the carbon footprint of projects. Their lightweight nature allows for efficient transportation, with a single truck carrying up to 320 feet of HDPE pipe compared to only 64 feet of reinforced concrete pipe. This efficiency lowers fuel consumption during delivery. Additionally, the production process of HDPE pipes requires less energy than traditional materials, resulting in reduced greenhouse gas emissions. Their long service life minimizes the need for replacements, further conserving resources and reducing environmental impact.
Recyclable Material
At the end of their lifecycle, HDPE pipes can be recycled into new products, supporting a circular economy. This recyclability reduces waste and conserves raw materials. Moreover, the material’s resistance to chemical leaching ensures that it does not contaminate the environment during use or disposal. These attributes make HDPE pipes an environmentally friendly choice for modern infrastructure projects.