HDPE pipe, short for High-Density Polyethylene pipe, is a modern solution for transporting fluids and gases. Its primary purpose is to provide a durable and versatile alternative to traditional piping materials. You’ll find it widely used in industries like water supply, gas distribution, and agriculture due to its unique properties.
The global demand for HDPE pipes continues to grow. For example, the market size is projected to increase from $21.7 billion in 2022 to $35.4 billion by 2032, with a steady annual growth rate of 5.1%. This rise reflects its reliability and adaptability in meeting diverse industrial needs.
Key Takeaways
HDPE pipes are strong and can last 50 to 100 years.
They are a good choice for long-term use in many areas.
These pipes bend easily, making them simple to install.
Fewer extra parts are needed, saving time and money.
HDPE pipes do not rust or get damaged by chemicals.
They keep fluids safe and clean during transportation.
These pipes are eco-friendly because they can be recycled.
Making them uses less energy than older pipe materials.
Using HDPE pipes saves money over time with low upkeep.
Their long life also helps reduce replacement costs.
What is HDPE Pipe?
Material Composition and Properties
HDPE pipe is made from high-density polyethylene, a thermoplastic polymer known for its exceptional strength and versatility. This material offers several key properties that make it ideal for piping systems:
Its chemical resistance prevents corrosion, reducing maintenance needs and extending the pipe’s lifespan.
The flexibility of HDPE allows it to handle ground movements and pressure changes without cracking.
It has a tensile strength of over 3500 psi, making it lightweight yet incredibly durable.
The low thermal coefficient of expansion ensures stability even in fluctuating temperatures.
HDPE’s molecular structure provides a high strength-to-weight ratio, enabling it to withstand physical impacts and chemical exposure.
These properties make HDPE pipes suitable for applications ranging from water distribution to industrial systems.
How HDPE Pipes Are Manufactured
The manufacturing process of HDPE pipes involves several precise steps to ensure quality and consistency:
Polyethylene pellets are dried in a hopper to remove moisture.
A vacuum pump transfers the dried material into a blender.
The material is heated to around 356°F in a barrel heater until it becomes molten.
The molten polyethylene is shaped into a cylindrical form using a die mold.
The pipe is cooled in a tank where water is sprayed in stages to solidify it.
This process ensures uniform wall thickness and strength, which are critical for the pipe’s performance in various environments.
Why HDPE Is a Popular Material for Pipes
HDPE pipe has gained popularity due to its unmatched benefits:
It resists corrosion, abrasion, and chemical degradation, ensuring long-term durability.
Its flexibility allows for easy installation and reduces the risk of leaks.
The material absorbs impacts without breaking, making it suitable for high-traffic or underground applications.
Although the initial cost may be higher, HDPE pipes require less maintenance and last longer, offering cost savings over time.
HDPE is recyclable and has a lower carbon footprint compared to other materials, making it an environmentally friendly choice.
These advantages make HDPE pipes a reliable and sustainable option for modern infrastructure projects.
Key Features of HDPE Pipes
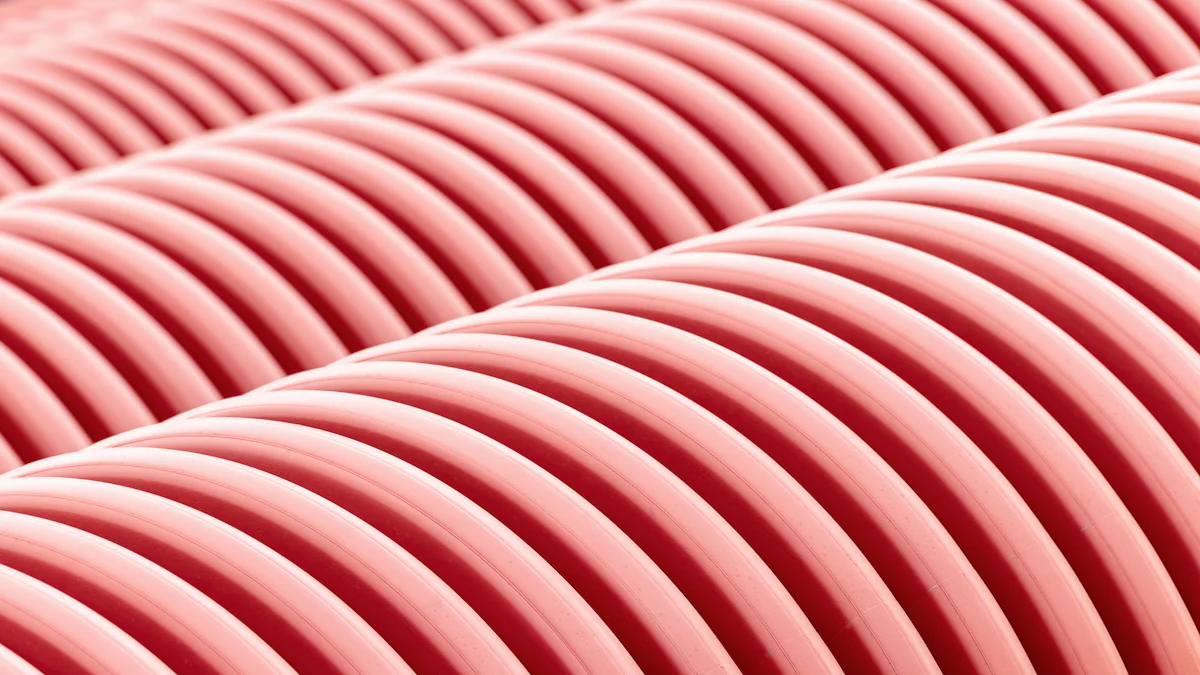
Durability and Longevity
HDPE pipes are built to last. Their lifespan ranges from 50 to 100 years, outperforming many traditional materials. For comparison, PVC pipes typically last 50 to 70 years, while galvanized steel may only last 30 to 50 years.
Pipe Material | Estimated Lifespan |
---|---|
High-density Polyethylene (HDPE) | 50 to 100 years |
Polyvinyl Chloride (PVC) | 50 to 70 years |
Reinforced Concrete Pipes (RCP) | 75 to 100 years |
Scientific tests further highlight their durability. For instance, a 16-inch HDPE pipe underwent two million cycles of pressure testing at 1.5 times its pressure class without failure. This simulates 100 years of service under extreme conditions. Such resilience ensures you can rely on HDPE pipes for long-term use, even in demanding environments.
Flexibility and Lightweight Design
The flexibility of HDPE pipes makes them a practical choice for many applications. They can bend up to 25 degrees without losing structural integrity, reducing the need for additional fittings by about 30%. This feature simplifies installation and lowers material costs.
You’ll also find that HDPE pipes are lightweight, making them easier to handle and transport. In one project for the San Antonio Water System, crews fused long sections of HDPE pipe above ground, speeding up installation and cutting costs. This flexibility and lightweight design save time and money during installation and maintenance.
Corrosion and Chemical Resistance
HDPE pipes resist corrosion and chemical damage, making them ideal for industrial and environmental applications. Unlike metal pipes, they won’t rust or degrade when exposed to moisture or harsh chemicals.
Application Type | Chemicals Resisted |
---|---|
Acid/Caustic Lines | Strong acids and bases |
Organic Chemicals | Various organic solvents |
Inorganic Chemicals | Various inorganic compounds |
Hazardous Waste | Multiple hazardous materials |
Wastewater | Contaminated water |
This resistance allows HDPE pipes to handle strong acids, bases, and other hazardous materials effectively. Whether you’re working with industrial wastewater or chemical fertilizers, HDPE pipes provide a reliable and long-lasting solution.
Leak-Free and Secure Connections
HDPE pipes are known for their ability to create leak-free and secure connections, making them a reliable choice for fluid and gas transportation. Unlike traditional materials that rely on mechanical fittings prone to wear and tear, HDPE pipes use advanced welding techniques to form seamless joints. These methods ensure a strong bond that eliminates weak points where leaks could occur.
Here are the key engineering mechanisms behind these connections:
Extrusion welding: This method applies heat to the joint area, melting the material and creating a robust connection.
Butt welding: The most common technique, it uses heat to fuse the ends of two pipes, forming a continuous and durable joint.
Socket welding: One pipe is inserted into another, and heat is applied to weld them together.
Electro-fusion welding: Electric heating elements embedded in special fittings melt the pipe surfaces, ensuring a precise and secure bond.
To achieve leak-free connections, you must follow best practices during installation:
Select HDPE pipes and fittings that match the working conditions of your project.
Clean and prepare the pipe surfaces to remove impurities that could weaken the weld.
Use qualified personnel to perform the welding, as accuracy is critical for reliability.
Conduct pressure tests on completed joints to verify their strength and ensure no leaks.
These steps guarantee that your HDPE piping system performs efficiently and remains leak-proof over its lifespan. By investing in proper installation techniques, you can avoid costly repairs and downtime. This makes HDPE pipes a dependable solution for both small-scale and large-scale applications.
💡 Tip: Always consult with certified professionals when installing HDPE pipes to maximize their performance and durability.
Common Uses of HDPE Pipes
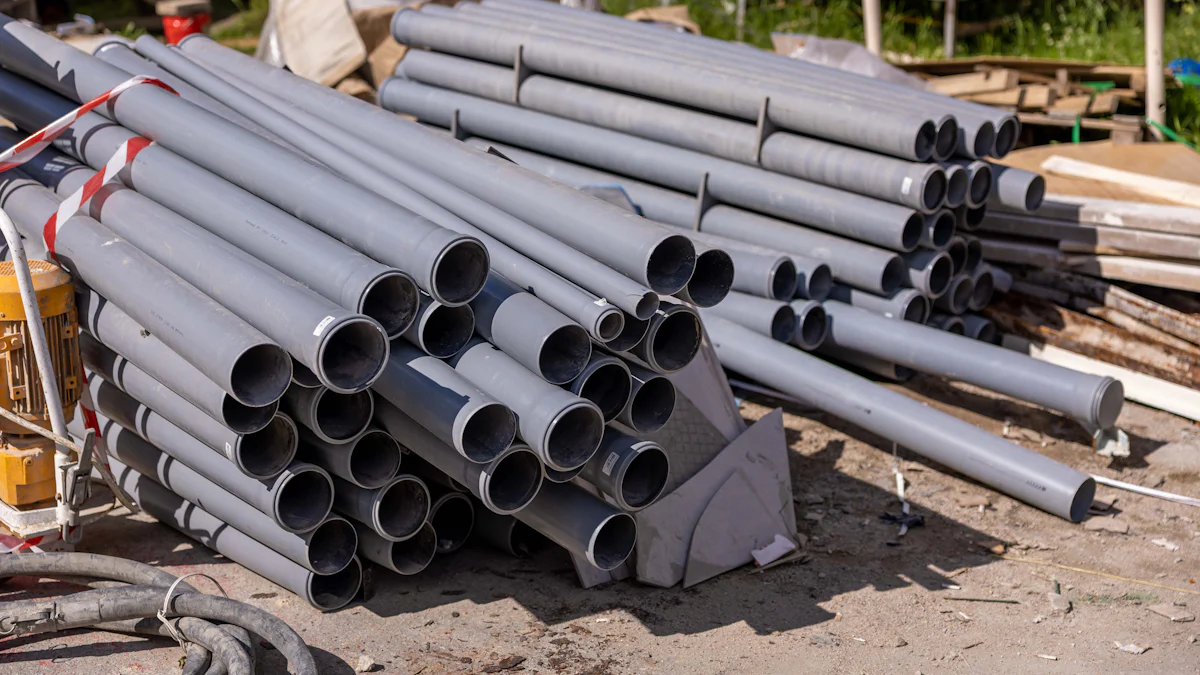
Water Supply and Distribution
HDPE pipes play a vital role in water supply systems. Their durability and resistance to corrosion make them ideal for transporting clean water over long distances. Unlike traditional materials, they do not rust or degrade, ensuring the water remains uncontaminated. Municipal water systems often rely on HDPE pipes for their ability to handle high pressure and fluctuating temperatures.
You’ll also appreciate their flexibility during installation. HDPE pipes can bend around obstacles, reducing the need for additional fittings. This feature simplifies the process and lowers costs. Their lightweight design further enhances efficiency, allowing for quicker transportation and installation. Whether for urban water distribution or rural supply networks, HDPE pipes provide a reliable and long-lasting solution.
Gas and Oil Transportation
HDPE pipes excel in gas and oil transportation due to their unique properties. They withstand extreme temperatures and pressures, making them suitable for challenging environments. Their resistance to corrosion and chemicals ensures they remain unaffected by harsh substances or environmental factors like UV rays.
Here’s why HDPE pipes outperform traditional materials in this sector:
They maintain structural integrity under high pressures.
Their flexibility allows for easy adaptation to terrain changes.
Leak-free joints ensure safe and efficient transportation.
The material is eco-friendly and has a long service life.
These features make HDPE pipes a dependable choice for gas distribution networks and oil pipelines. You can trust them to deliver consistent performance while minimizing maintenance needs.
Sewage and Drainage Systems
HDPE pipes are a top choice for sewage and drainage systems. Their chemical resistance allows them to handle wastewater and hazardous materials without degrading. Proper fusion techniques create leak-free joints, preventing environmental contamination.
Using HDPE pipes in these systems also offers environmental benefits:
Energy-efficient production reduces resource consumption.
These advantages make HDPE pipes an environmentally friendly and cost-effective option for managing sewage and drainage. Whether for municipal projects or industrial applications, they provide a sustainable and reliable solution.
Agricultural and Irrigation Applications
HDPE pipes have revolutionized agricultural irrigation systems by providing an efficient and reliable way to deliver water to crops. These pipes are essential for modern farming, as they transport water from sources like wells, rivers, and reservoirs directly to fields. Their flexibility and lightweight design make them easy to install, even in challenging terrains. You can use them for drip irrigation, sprinkler systems, or flood irrigation, depending on your specific needs.
One of the key advantages of HDPE pipes in agriculture is their ability to withstand harsh environmental conditions. They resist UV radiation, ensuring durability even under prolonged sun exposure. Their chemical resistance also allows them to handle fertilizers and pesticides without degrading. This ensures that your irrigation system remains functional and efficient for years.
The global adoption of HDPE pipes in agriculture highlights their importance. Farmers worldwide rely on these pipes to conserve water and improve crop yields. By reducing water loss through leaks or evaporation, HDPE pipes help you optimize water usage. This is especially critical in regions facing water scarcity. Whether you manage a small farm or a large agricultural operation, HDPE pipes offer a sustainable and cost-effective solution for irrigation.
🌱 Did You Know? HDPE pipes are not only durable but also environmentally friendly. Their recyclability makes them a sustainable choice for agricultural applications.
Industrial and Mining Operations
HDPE pipes excel in industrial and mining operations due to their ability to handle extreme conditions. They outperform traditional materials like steel, especially when transporting abrasive slurries. For example, HDPE pipes last up to four times longer than steel pipes in such applications. This durability reduces the need for frequent replacements, saving you both time and money.
In mining, HDPE pipes have proven their reliability in transporting thickened tailings. At the Cerro Negro Norte Mine in Chile, these pipes carry tailings with a solid concentration of 65% over long distances. Similarly, in Peru’s Toromocho copper project, HDPE pipes handle approximately 140,000 metric tonnes of highly viscous tailings daily. Their flexibility and resistance to wear make them ideal for these demanding tasks.
Mining operations also benefit from the cost advantages of HDPE pipes. They lower both capital and operational expenses, making them a practical choice for large-scale projects. However, joining HDPE pipes in confined spaces can be challenging. Proper planning and skilled personnel are essential to ensure secure connections in such environments.
Whether you’re managing industrial wastewater or transporting mining tailings, HDPE pipes provide a dependable and efficient solution. Their ability to handle harsh chemicals, high pressures, and abrasive materials makes them a top choice for industrial and mining applications.
💡 Tip: When using HDPE pipes in mining, consider electro-fusion welding for secure and leak-free joints, even in tough conditions.
Why Use HDPE Pipes?
Cost-Effectiveness and Long-Term Savings
HDPE pipes offer significant cost advantages over time. While their initial price may be higher than materials like PVC or steel, their durability and low maintenance requirements make them a smart investment. For example, a 1-inch IPS SDR11 HDPE pipe costs between $1.50 and $2.50 per foot. This upfront cost reflects the long-term value you gain from their extended lifespan.
These pipes last 50 to 100 years, far outliving galvanized steel pipes, which typically last only 40 to 50 years. This longevity reduces the need for frequent replacements, saving you money on labor and materials. Additionally, HDPE pipes resist scaling and bacteriological activity, which minimizes cleaning and maintenance costs. Their seamless connections also prevent leaks, reducing environmental discharge issues and repair expenses.
In one project in India, an HDPE pipeline cost $129,382, while a comparable mild steel pipeline would have cost nearly $299,000. The lightweight nature of HDPE further lowers installation costs by reducing labor requirements. Over a 10-year period, these savings add up, making HDPE pipes a cost-effective choice for various applications.
Environmental Sustainability
HDPE pipes stand out as an environmentally friendly option. Their production consumes less energy compared to traditional materials, and their recyclability reduces landfill waste. In 2020, HDPE pipes had a recycling rate of 33%, significantly higher than PVC pipes, which had a rate of less than 1%.
These pipes also meet several environmental standards, ensuring their safety and sustainability. For instance, they comply with NSF/ANSI 61 for drinking water safety and EN 12201-2 for water supply and drainage systems. Their resistance to corrosion and chemicals prevents contamination, making them ideal for eco-conscious projects. By choosing HDPE pipes, you contribute to a greener future while benefiting from their durability and efficiency.
Standard | Description |
---|---|
EN 12201-2 | European standard for plastic piping systems for water supply and drainage under pressure. |
ASTM F714 | Covers HDPE pipe based on outside diameter control for general purpose and water applications. |
NSF/ANSI 61 | Health effects standard for chemicals and products in contact with drinking water. |
API 15LE | Standard for polyethylene line pipe and tubing relevant for oil and gas applications. |
Versatility Across Applications
HDPE pipes excel in a wide range of applications, making them one of the most versatile piping solutions available. Their corrosion resistance ensures safe delivery of potable water, while their flexibility allows them to adapt to urban sewage systems with minimal excavation. In industrial processes, they handle high pressure and chemical exposure effectively.
You’ll also find HDPE pipes used in telecommunications to protect cables from impact and corrosion. In earthquake-prone areas, their flexibility helps them withstand ground movements without breaking. Whether for geothermal heating systems, gas pipelines, or agricultural irrigation, HDPE pipes deliver reliable performance. Their ability to handle diverse conditions makes them a preferred choice across industries.
🌍 Note: By using HDPE pipes, you not only benefit from their versatility but also support sustainable practices in infrastructure development.
High Performance and Reliability
HDPE pipes deliver exceptional performance and reliability, even in the most demanding conditions. Their design ensures long-term effectiveness, making them a trusted choice for critical applications. You can rely on HDPE pipes to resist corrosion and chemical attacks, which reduces maintenance needs and ensures consistent flow capacity. Unlike other materials, they resist fouling and buildup, maintaining their efficiency over time.
Metric | Description |
---|---|
Temperature Tolerance | Functions in extreme hot and cold conditions (-40°C to 80°C), wider range than most metal pipes. |
Flexibility | Can deflect up to 7.5% without damage, compared to 0.5% for rigid pipes, reducing installation costs. |
Wear Resistance | Up to 4 times longer service life than steel pipes in abrasive slurry applications. |
Pressure Capacity | Can handle pressures up to 250 psi or higher, maintaining performance over decades. |
The unique features of HDPE pipes contribute to their high performance. Their flexibility allows them to bend without breaking, reducing the need for additional fittings. This adaptability also makes installation faster and more cost-effective. Their wear resistance ensures they last longer than steel pipes, especially in abrasive environments.
Strength and Durability: HDPE pipes withstand impacts, harsh weather, and corrosion, extending their lifespan significantly.
Flexibility: Lightweight and heat-fused joints create strong, durable connections.
Cost Savings: Their durability and ease of installation reduce long-term expenses.
Real-world examples highlight their reliability. After the Kobe earthquake in Japan, HDPE pipes had a failure rate of nearly 0, while other materials experienced up to 1.1 failures per mile. This demonstrates their ability to perform under extreme conditions, ensuring uninterrupted service when you need it most.
💡 Tip: HDPE pipes are an excellent choice for projects requiring durability and consistent performance, even in harsh environments.
HDPE pipes redefine durability and efficiency in piping systems. Their corrosion resistance and lifespan of up to 100 years make them a cost-effective choice for infrastructure projects. You’ll find them indispensable across industries like water supply, agriculture, and industrial operations due to their flexibility and chemical resistance. Compared to traditional materials, HDPE pipes reduce maintenance costs by 40% and minimize environmental impact through recyclability and energy-efficient production. With a market projected to reach $35.4 billion by 2032, HDPE pipes continue to lead sustainable development. Choose HDPE pipes for reliability, performance, and long-term savings.
FAQ
What makes HDPE pipes better than traditional materials?
HDPE pipes outperform traditional materials due to their flexibility, corrosion resistance, and long lifespan. They handle extreme conditions without cracking or degrading. Unlike metal pipes, they resist rust and chemical damage, making them a cost-effective and durable choice for various applications.
Can HDPE pipes be used for drinking water?
Yes, HDPE pipes are safe for drinking water. They meet NSF/ANSI 61 standards, ensuring no harmful chemicals leach into the water. Their smooth interior prevents bacterial growth, maintaining water quality. You can trust HDPE pipes for clean and safe water distribution.
How do you join HDPE pipes securely?
You can join HDPE pipes using welding techniques like butt fusion, electro-fusion, or socket welding. These methods create seamless, leak-free joints. Proper surface preparation and skilled personnel ensure strong connections. Always follow manufacturer guidelines for the best results.
Are HDPE pipes environmentally friendly?
HDPE pipes are eco-friendly. Their production uses less energy, and they are 100% recyclable. They reduce waste and have a lower carbon footprint compared to traditional materials. By choosing HDPE, you support sustainable infrastructure development.
What is the lifespan of HDPE pipes?
HDPE pipes last 50 to 100 years, depending on usage and environmental conditions. Their durability reduces the need for frequent replacements, saving you money and resources. Proper installation and maintenance further extend their lifespan.